Trusted by startups and Fortune companies
Capabilities of Our Product Operations Management Software
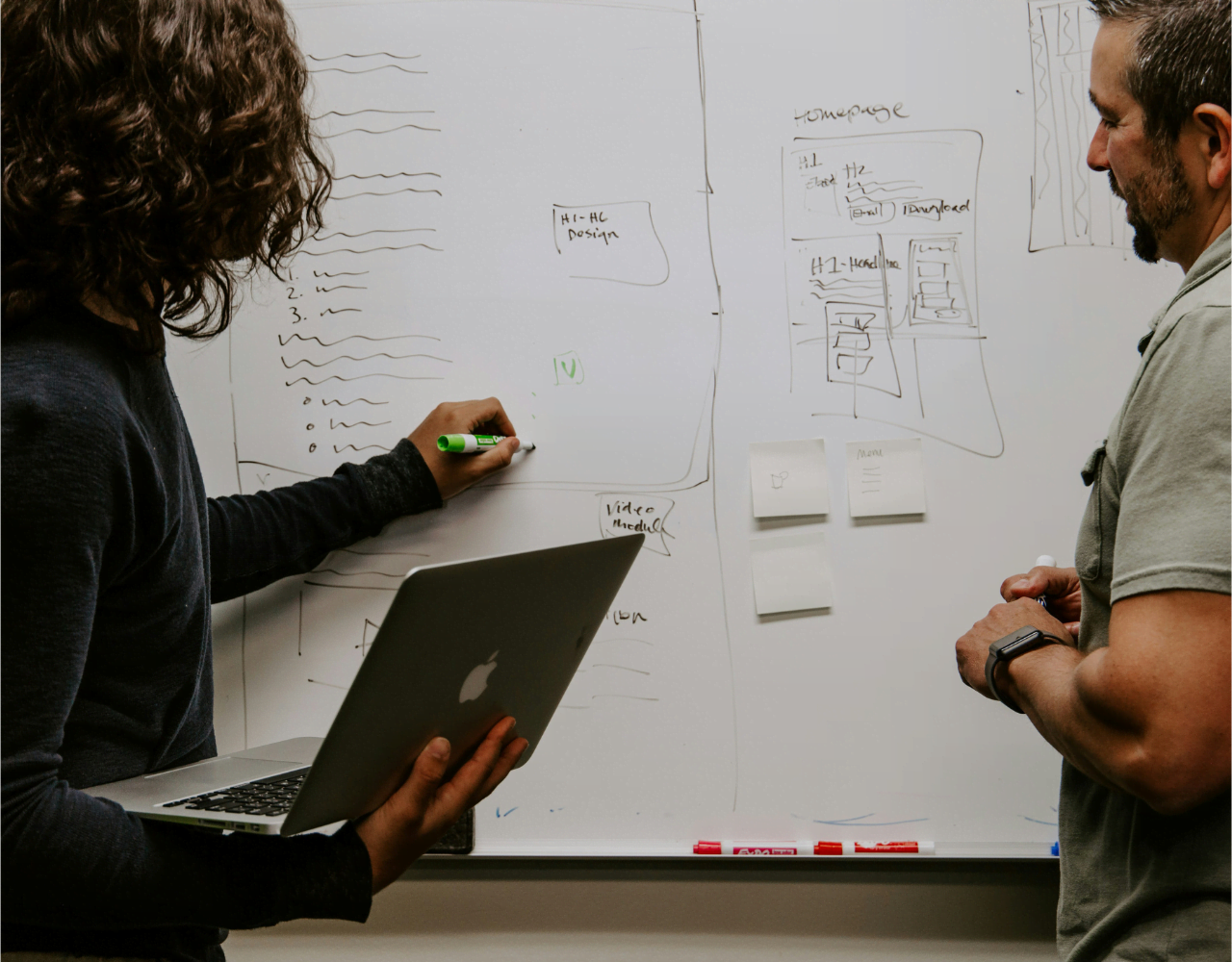
- Utilize tools for setting and monitoring production targets.
- Implement material requirements planning.
- Flexibly adjust production schedules as needed.
- Harness AI for process enhancement.
- Efficiently manage inventory across multiple locations.
- Handle orders comprehensively from creation to costing.
- Ensure timely and cost-effective production processes.
- Monitor inventory in real-time.
- Set alerts for low stock levels.
- Utilize AI for storage optimization suggestions.
- Streamline order picking and packing processes.
- Track sales orders from initiation to fulfillment.
- Manage invoices and purchase orders seamlessly.
- Automate purchase order processes for efficiency.
- Track requests and automate approval workflows.
- Scheduled regular maintenance
- Real-time equipment status monitoring
- Implementing quality control charts
- Scheduling regular quality checks
- Scheduling and reporting on performance
- Facilitating instant team communication
- Harnessing predictive analytics for product demand forecasts
- Analyzing production capacity and outputs for optimized operations
Ready to Innovate?
Let's co-create groundbreaking products together, merging your vision with our expertise for unparalleled results.
Get StartedIndustries We Serve
Our expertise extends to manufacturing industries seeking to enhance production and warehouse efficiency, streamline equipment maintenance, manage procurement and sales, and optimize workforce operations.
Additionally, we cater to service-oriented and project-centric enterprises aiming to refine service processes, enhance HR and project management, streamline service requests and supply chain operations, and manage travel and expenses effectively.
Service Operations Management Software: Key Features
Our suite of service operations management solutions is tailored to meet the varied project requirements of businesses. We specialize in optimizing the daily workflows of operations and resource managers, project managers, and service delivery teams. Here, we outline the distinctive features of our software.
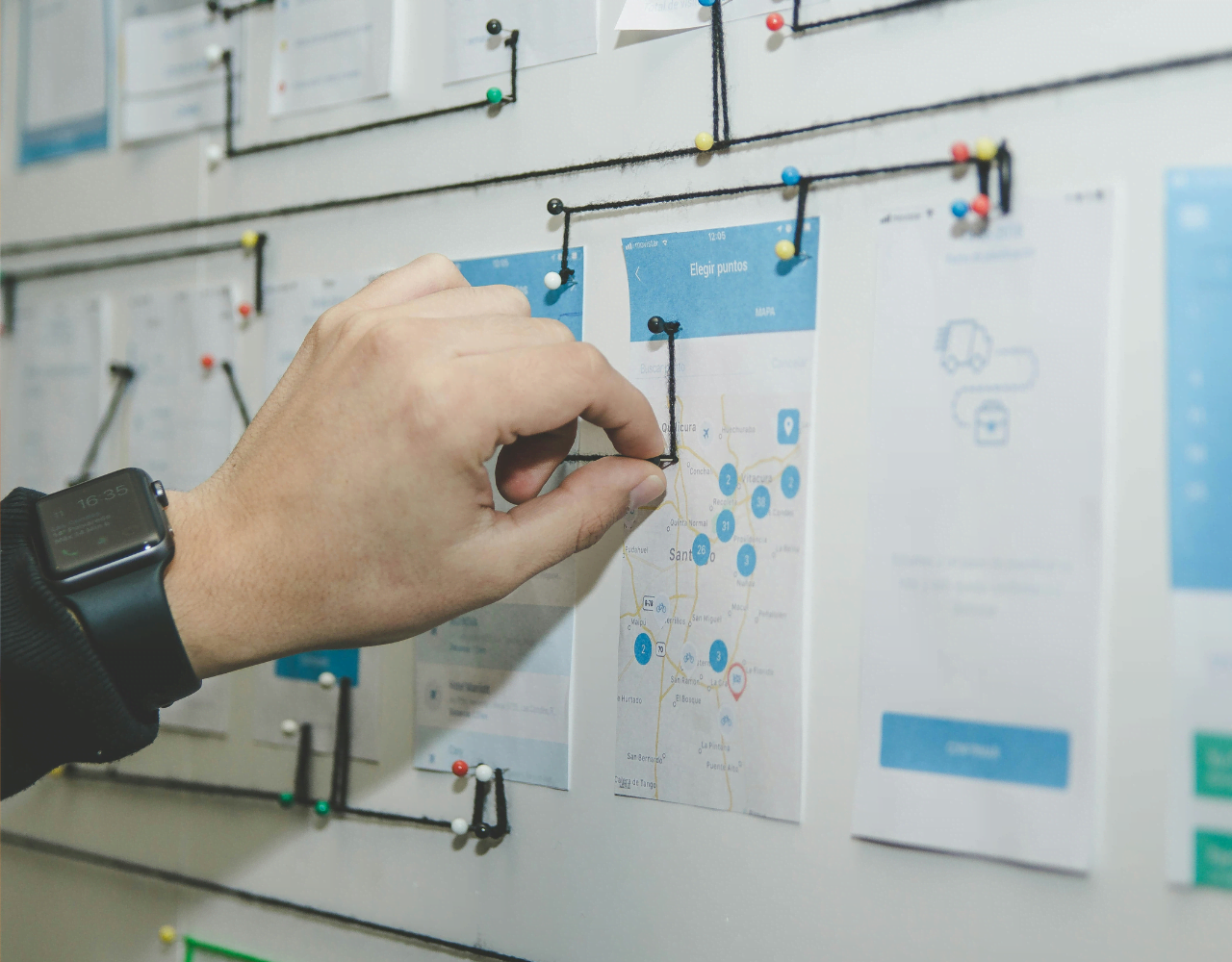
- Utilize barcode-based tracking for supplies
- Streamline purchase order creation
- Track real-time status updates
- Establish comprehensive goals and track milestones
- Create, edit tasks, and estimate resources
- Customize progress and budget alerts
- Store service-related documents centrally
- Enable swift document retrieval with auto-referencing
- Enhance operational efficiency through organized information
- Analyze operational impacts and changes
- Forecast revenue and assess risks
- Drive strategic decision-making with data insights
- Customized service workflows and performance benchmarks
- Real-time dashboard monitoring of KPIs
- Iterative service improvement procedures
- Flexible timesheet management configurations
- Automated invoice generation for streamlined billing
- Efficient monitoring of working hours
- Centralized, up-to-date employee profiles
- AI-driven recommendations for resource allocation
- Real-time monitoring of team capacity
- Methodical task and request assignment
- Real-time progress monitoring
- Comprehensive tracking of employee work
Consolidate all your operations management needs with us.
From process enhancement and project oversight to resource allocation and data analysis, we've got you covered.
Our comprehensive solutions encompass everything you need, whether it's refining current operations or building from the ground up.
- Access India's Top 1% Software Talent
- Trusted by Startups to Fortune 500 companies
- Seamless process from concept to deployment
- Global presence with timezone-friendly service
- State-of-the-art data security measures
- Timely delivery with no unexpected setbacks
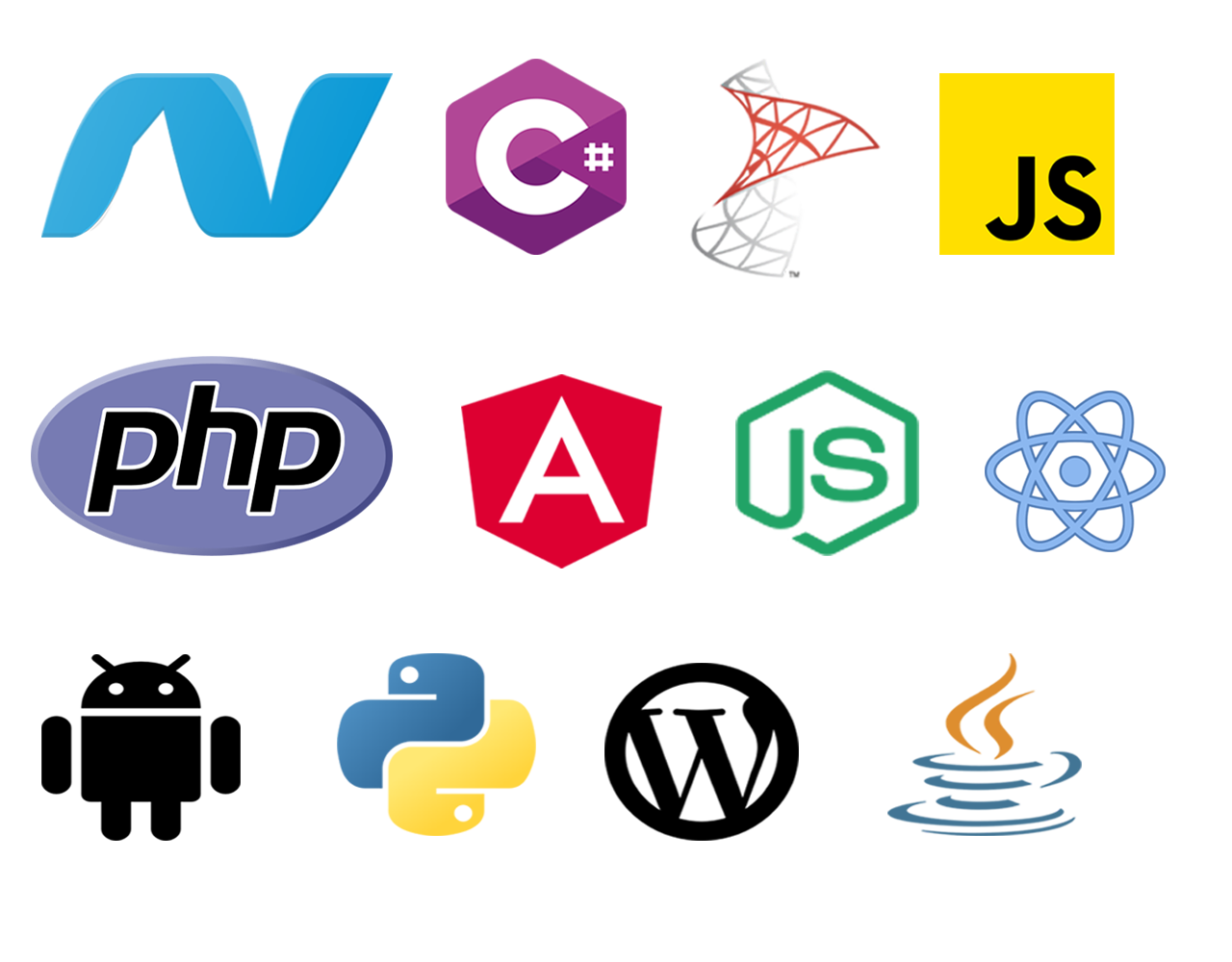
Ready to Innovate?
Let's co-create groundbreaking products together, merging your vision with our expertise for unparalleled results.
Get StartedNavigating the realm of operations management
Guide Topics
Integrating your Production Operations Management System (POMS)
These integrations serve as crucial cogs in the wheel of Production Operations Management Systems (OMS), elevating efficiency and functionality:
- Business Intelligence (BI) tools: Uncover nuanced operational insights, empowering data-driven decisions and fostering continuous process refinement.
- Supply Chain Management (SCM) software: Seamlessly orchestrate procurement, order tracking, and production planning, ensuring seamless synchronization across the supply chain.
- Customer Relationship Management (CRM) software: Facilitate a seamless flow of customer orders, inventory updates, and production capacities, nurturing strong client relationships and efficient order fulfillment.
- Financial software: Safeguard financial integrity with meticulous accounting, cost control, and supplier payment management, fortifying fiscal transparency and accountability.
- Product Lifecycle Management (PLM) software: Automate the assimilation of design revisions and bill of materials (BOM), enabling agile and precise production planning and execution.
- Manufacturing Execution System (MES): Real-time oversight of production activities, facilitating agile execution of planned orders and stringent quality control measures.
- Human Resources Management (HRM) software: Optimize workforce allocation and task scheduling based on resource availability, fostering a harmonious balance between human capital and operational demands.
To know more about hiring a dedicated development team, read our detailed guide.
Varieties of Operations Management
Below are various categories of operations management:
- Manufacturing Operations Management: This area concentrates on coordinating and overseeing manufacturing processes, encompassing tasks such as production planning, scheduling, inventory management, quality control, and maintenance.
- Service Operations Management: This field entails the design and administration of service delivery processes, including aspects like service design, capacity planning, service quality management, customer relationship management, and performance assessment.
- Supply Chain Operations Management: This discipline is dedicated to enhancing activities across the supply chain, covering functions such as supplier management, demand forecasting, procurement, logistics, and distribution.
- Project Operations Management: This domain involves the planning, execution, and monitoring of projects, which encompasses tasks like project planning, resource allocation, scheduling, risk management, and performance tracking.
- Quality Operations Management: This sector ensures that products or services consistently meet or exceed customer expectations, involving activities like quality planning, control, assurance, and ongoing improvement.
- Maintenance Operations Management: This area focuses on planning and executing maintenance tasks to optimize the performance and extend the lifespan of assets and facilities.
Want to look for more benefits of hiring dedicated web development teams? Read our blog.
Lean operations and Just-in-Time (JIT) inventory management
Lean operations and Just-in-Time (JIT) inventory management offer numerous advantages to businesses:
- Cost Reduction: By eliminating waste and excess inventory, lean operations and JIT inventory management reduce carrying costs and overhead expenses, leading to significant cost savings.
- Improved Efficiency: JIT ensures that materials and resources are available precisely when needed, minimizing idle time and enhancing production efficiency.
- Reduced Lead Times: Shortened lead times through JIT enable faster response to customer demands, reducing order-to-delivery cycles and improving customer satisfaction.
- Enhanced Quality: Lean processes prioritize quality control, resulting in fewer defects and higher product quality, ultimately leading to greater customer satisfaction.
- Increased Flexibility: JIT enables businesses to adapt quickly to changing market conditions and customer preferences, maintaining competitiveness in dynamic environments.
- Optimized Space Utilization: Reduced inventory levels free up storage space, allowing for more efficient use of facilities and resources.
- Better Supplier Relationships: JIT fosters closer collaboration with suppliers, leading to improved communication, reliability, and timeliness in deliveries.
- Waste Reduction: Lean principles identify and eliminate various forms of waste, such as overproduction and unnecessary processing, contributing to resource optimization and sustainability.
- Customer Satisfaction: JIT ensures on-time delivery and high-quality products, enhancing customer satisfaction and loyalty.
- Higher Profit Margins: The combination of cost savings, efficiency improvements, and waste reduction leads to higher profit margins and improved financial performance.
Lean operations and Just-in-Time (JIT) inventory management
Operations management is a dynamic field that constantly evolves with emerging trends and innovations. Here are some of the latest developments shaping the landscape:
- Digital Transformation: Businesses are increasingly leveraging advanced technologies such as artificial intelligence (AI), machine learning, Internet of Things (IoT), and data analytics to streamline processes, enhance decision-making, and improve supply chain visibility.
- Supply Chain Resilience: There's a growing emphasis on building resilient supply chains capable of withstanding disruptions through risk assessment, diversification, and real-time monitoring.
- Sustainability Practices: Integrating eco-friendly practices into operations management, including sustainable sourcing, waste reduction, and carbon footprint reduction, to address environmental concerns.
- Circular Economy: Embracing circular economy principles to minimize waste and maximize the reuse, recycling, and refurbishment of products and materials.
- Blockchain Integration: Implementing blockchain technology for transparent and secure supply chain management, particularly in industries like food and pharmaceuticals.
- Predictive Maintenance: Utilizing predictive analytics and IoT sensors to monitor equipment health and proactively address maintenance needs, reducing downtime and costs.
- Remote Workforce Management: Employing technology to efficiently manage remote teams and maintain productivity, especially in response to global disruptions like the COVID-19 pandemic.
- E-commerce Optimization: Optimizing e-commerce operations, including inventory management, order fulfillment, and last-mile delivery, to meet the increasing demand for online shopping.
- 3D Printing: Exploring the potential of 3D printing for on-demand manufacturing, which can reduce lead times and enable customization.
- Augmented Reality (AR) and Virtual Reality (VR): Using AR and VR technologies for employee training, remote assistance, and improving operational efficiency.
- Robotic Process Automation (RPA): Automating routine tasks and processes using software robots to enhance accuracy and reduce labor costs.
- Big Data Analytics: Harnessing big data to gain insights into customer behavior, market trends, and operational performance for informed decision-making.
- Lean and Agile Approaches: Combining lean principles with agile methodologies to enable quick adaptation to changing customer demands and market conditions.
- Ethical and Responsible Operations: Prioritizing ethical practices, fair labor, and responsible sourcing to meet consumer demands for socially conscious products.
Frequently Asked Questions
- Business Intelligence (BI) Tool Integration
- Supply Chain Management (SCM) Integration
- Customer Relationship Management (CRM) Integration
- Financial Software Integration
- Product Lifecycle Management (PLM) Integration
- Manufacturing Execution System (MES) Integration
- Human Resources Management (HRM) Integration
These integrations streamline processes, enhance visibility, and improve efficiency to meet your specific business needs.
Client Feedback on Our Services
We sincerely appreciate the trust our clients place in us and take pride in providing quality solutions that surpass their expectations. Here's what some of them have to say about their experiences: